Skip

In the ever-evolving world of technology, one innovation that has captured the attention of enthusiasts and experts alike is the programmable logic controller (PLC). This versatile device has revolutionized industrial automation, offering unparalleled control and flexibility. In this comprehensive article, we delve into the intricacies of PLCs, exploring their history, functionality, and impact on various industries. By the end, you'll have a deep understanding of these powerful controllers and their role in shaping the future of automation.
The Evolution of Programmable Logic Controllers
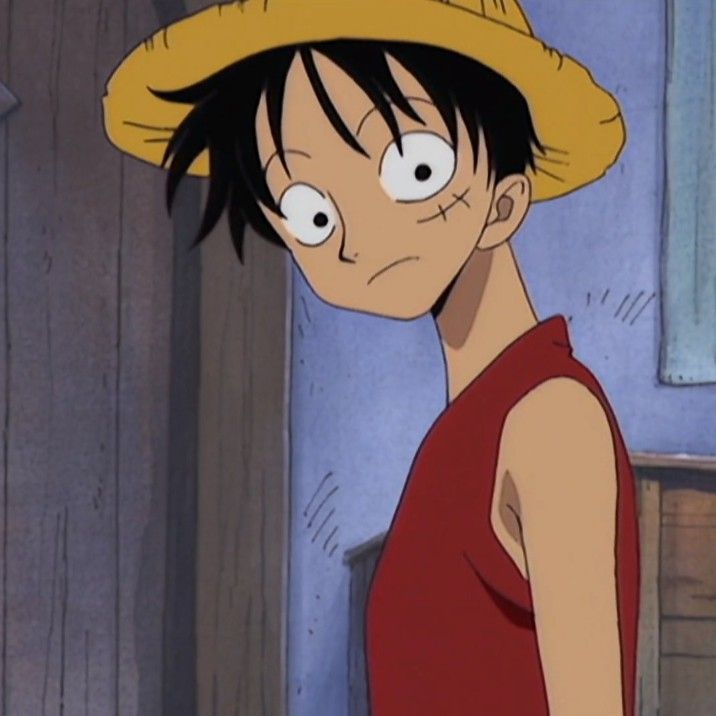
The journey of PLCs began in the 1960s when the need for flexible and programmable control systems arose in the manufacturing industry. Traditional hard-wired relay systems, though reliable, lacked the adaptability required for modern production lines. Enter the pioneers of PLC technology, who envisioned a more efficient and dynamic approach to automation.
Early PLCs were basic in comparison to today's standards, often featuring simple relay logic and limited programming capabilities. However, their introduction marked a significant shift towards more intelligent and programmable control systems. As technology advanced, so did the capabilities of PLCs, leading to the development of more complex and powerful devices.
Over the decades, PLCs have undergone numerous iterations, each generation bringing enhanced processing power, memory capacity, and programming flexibility. The introduction of microprocessors in the 1970s was a pivotal moment, allowing for more sophisticated programming and the ability to handle complex automation tasks.
Today, PLCs are an integral part of countless industrial applications, from manufacturing and robotics to energy management and transportation systems. Their ability to adapt to changing requirements and integrate seamlessly with other control systems has solidified their position as a cornerstone of modern automation.
Understanding PLC Functionality
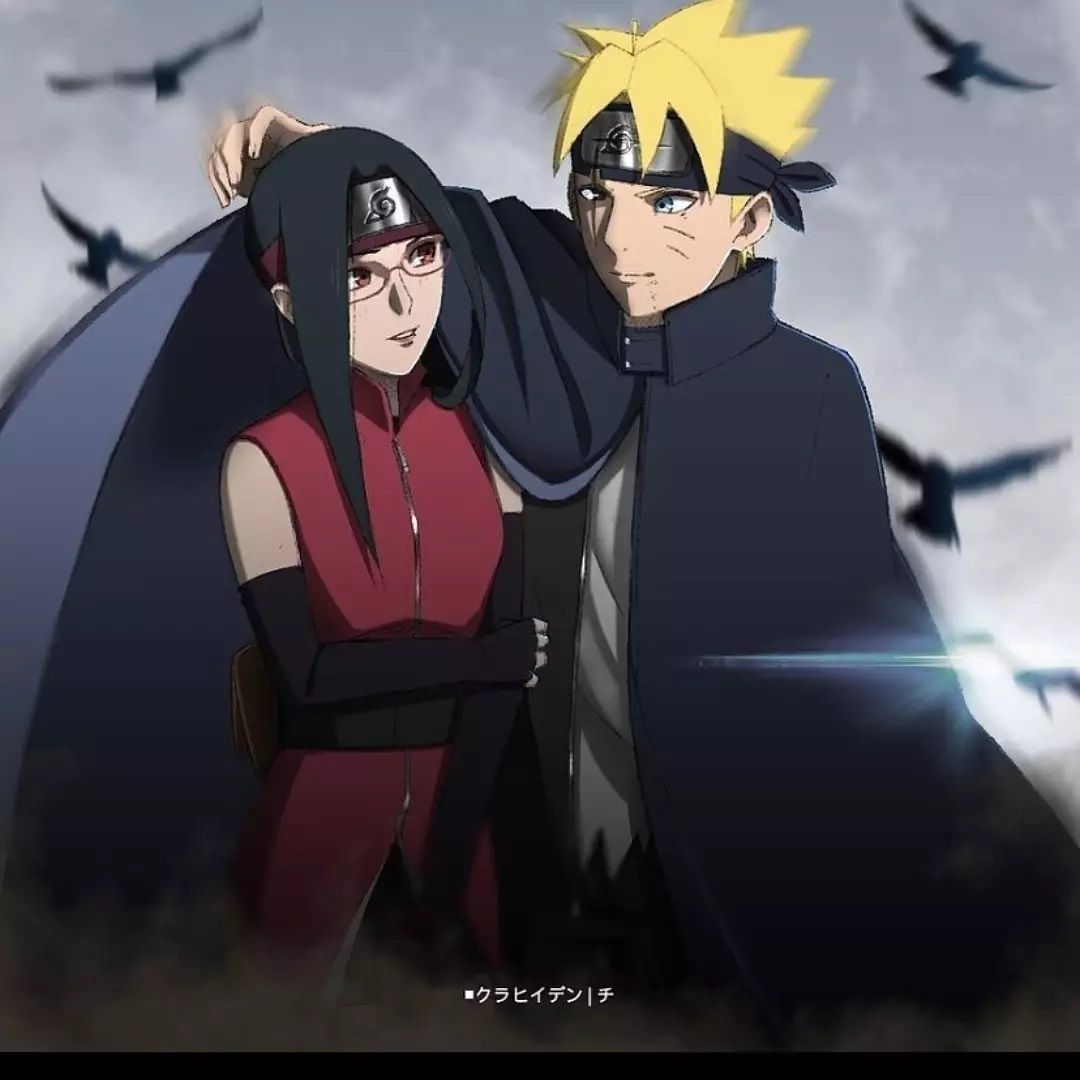
At its core, a PLC is a specialized computer designed to control and automate various processes and machinery. It receives input signals from sensors or other devices, processes this information based on a predefined program, and then outputs commands to control the connected machinery or systems.
PLCs offer several key advantages over traditional control systems. Firstly, they provide immense flexibility in programming, allowing users to easily adapt to changing production needs or process requirements. This flexibility is particularly valuable in industries where products or processes evolve rapidly.
Secondly, PLCs are highly reliable and durable, designed to withstand harsh industrial environments. Their rugged construction and advanced error-handling capabilities ensure consistent performance and minimal downtime.
Furthermore, PLCs excel in their ability to integrate with other control systems and devices. They can communicate with sensors, actuators, and other controllers, facilitating seamless coordination of complex processes. This interoperability is a key factor in the efficiency and success of modern automation systems.
Key Components of a PLC
-
Central Processing Unit (CPU): The brain of the PLC, responsible for executing the control program and managing data flow.
-
Memory: Stores the control program, input/output data, and other critical information. Memory types include ROM, EEPROM, and RAM.
-
Input/Output (I/O) Modules: Interface between the PLC and external devices, allowing it to receive input signals and send output commands.
-
Power Supply: Provides the necessary electrical power to operate the PLC and its components.
-
Programming Device: Allows users to create and upload control programs to the PLC, often through a dedicated programming software.
These components work in harmony to provide precise control and automation, making PLCs an indispensable tool in a wide range of industries.
Applications and Industries Transformed by PLCs
The impact of PLCs extends across numerous sectors, revolutionizing the way processes are controlled and optimized. Here are some key industries where PLCs have made a significant difference:
Manufacturing
PLCs are ubiquitous in manufacturing, where they control and automate production lines, assembly processes, and quality control systems. Their ability to handle complex logic and respond to real-time data enables manufacturers to achieve higher production rates, improve product quality, and reduce waste.
Energy and Utilities
In the energy sector, PLCs play a critical role in managing power generation, distribution, and consumption. They control and monitor various processes, from turbine operations in power plants to smart grid management, ensuring efficient and reliable energy delivery.
Transportation and Logistics
PLCs are integral to transportation systems, controlling traffic signals, rail systems, and even autonomous vehicles. In logistics, they optimize warehouse operations, manage conveyor systems, and coordinate inventory control, enhancing efficiency and accuracy.
Water and Wastewater Treatment
PLCs ensure the smooth operation of water treatment plants, wastewater management systems, and irrigation networks. They control pumps, valves, and sensors, maintaining water quality and optimizing resource usage.
Food and Beverage Industry
In food processing plants, PLCs automate production lines, control packaging machinery, and ensure product quality and safety. Their precise control capabilities are vital in maintaining consistent product standards.
Mining and Minerals Processing
PLCs optimize mining operations by controlling equipment such as conveyors, crushers, and sorting systems. They enhance safety, improve efficiency, and reduce costs in this demanding industry.
These are just a few examples of how PLCs have transformed industries, but their impact extends far beyond these sectors. Their versatility and adaptability make them a key enabler of Industry 4.0 and the digital transformation of manufacturing and other sectors.
The Future of PLCs and Automation
As technology continues to advance, the future of PLCs and automation looks increasingly promising. Here are some key trends and developments shaping the future of this field:
Internet of Things (IoT) Integration
The IoT is rapidly transforming the way devices and systems interact. PLCs are becoming more connected, allowing them to communicate with a wide range of smart devices and sensors. This integration enhances data collection, analysis, and control, leading to more efficient and responsive automation systems.
Artificial Intelligence (AI) and Machine Learning
AI and machine learning technologies are being integrated into PLCs, enabling them to learn and adapt to changing conditions. This allows for more intelligent and autonomous decision-making, improving process efficiency and reducing human intervention.
Cyber-Physical Systems
Cyber-physical systems combine physical processes with computer-based algorithms, creating a seamless integration of the digital and physical worlds. PLCs are at the forefront of this development, acting as the bridge between the two realms and enabling advanced control and optimization.
Increased Miniaturization and Mobility
PLCs are becoming smaller and more compact, allowing for easier installation and integration into various systems. This miniaturization also opens up new applications in portable and mobile devices, expanding the reach of automation.
Enhanced Security Measures
With the increasing connectivity of PLCs, security becomes a critical concern. Manufacturers are developing more robust security features to protect against cyber threats, ensuring the integrity and safety of automation systems.
Conclusion
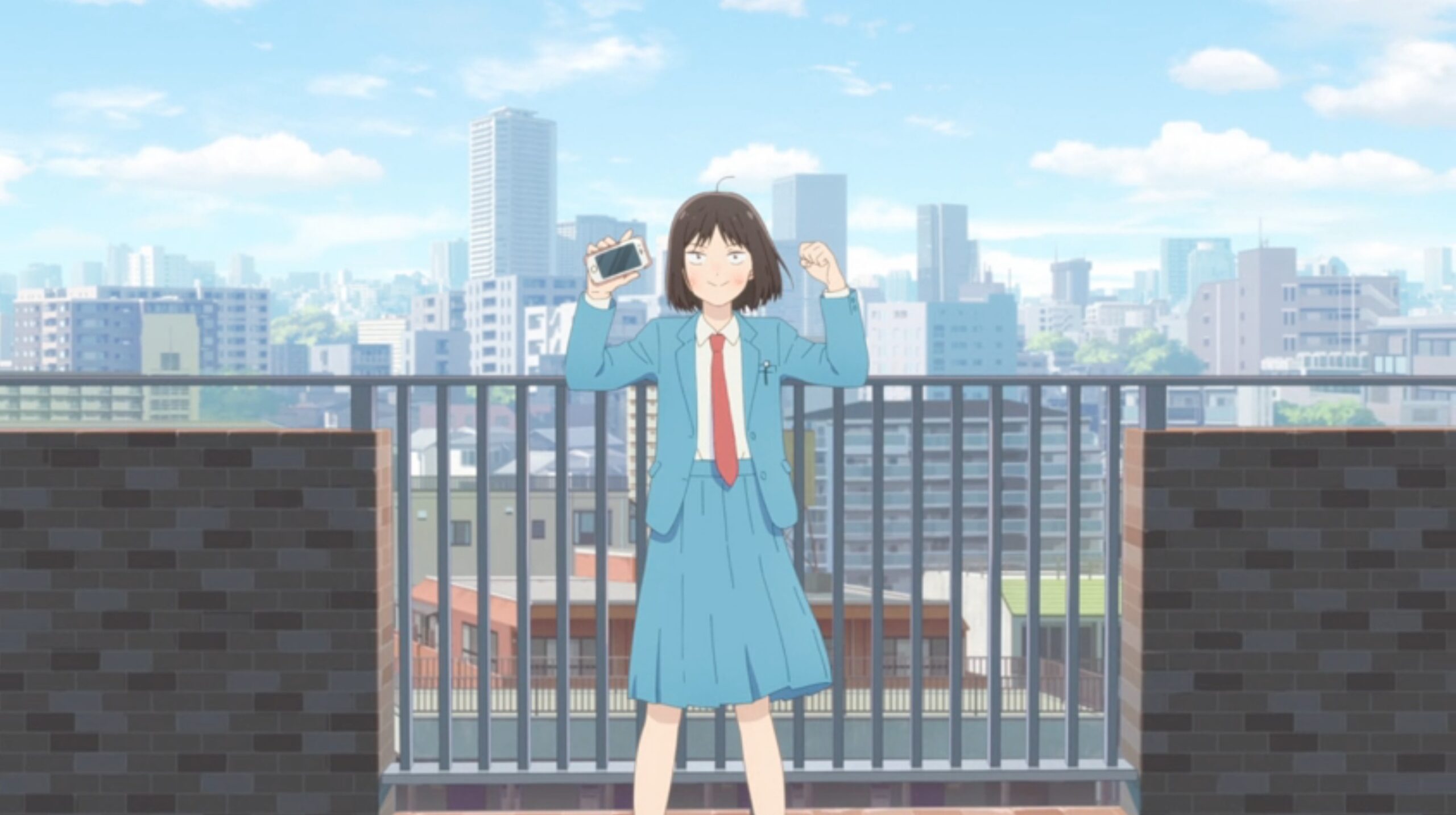
Programmable logic controllers have come a long way since their inception, evolving into powerful tools that drive the automation revolution. Their impact on various industries is profound, enabling greater efficiency, precision, and adaptability in processes and systems. As technology advances, PLCs will continue to play a pivotal role in shaping the future of automation, paving the way for a more connected and intelligent world.
How do PLCs compare to traditional control systems like relays and timers?
+PLCs offer several advantages over traditional control systems. They provide greater flexibility, allowing for easy programming and adaptation to changing requirements. Additionally, PLCs are more reliable, durable, and capable of handling complex logic and real-time data, making them ideal for modern automation needs.
What industries can benefit the most from implementing PLCs?
+PLCs are versatile and can benefit a wide range of industries. However, sectors such as manufacturing, energy, transportation, and water treatment often see significant improvements in efficiency, safety, and productivity by implementing PLCs. These industries rely heavily on precise control and automation, making PLCs an indispensable tool.
Are PLCs suitable for small-scale or home automation projects?
+Absolutely! While PLCs are commonly used in large-scale industrial applications, they can also be tailored for smaller projects. Miniaturized PLCs and microcontrollers offer cost-effective solutions for home automation, allowing users to control lighting, security systems, and even smart appliances.